On February 14, 2018, only 266 of the 870 KFC restaurants in the UK and Ireland remained open. Why? A fatal collision near their warehouse led to significant delays in procuring their ingredients. Next, DHL, KFC’s new logistics partner, failed to deliver essential ingredients from its single warehouse in Rugby.
Experts in the field of supply chain management have weighed in on the debacle. While operating from a single warehouse isn’t uncommon, the lack of contingency planning and the complexities of food distribution made the situation worse. Could manufacturing analytics have made a difference? Yes – a big one!
By leveraging real-time data and predictive analytics, KFC could have identified vulnerabilities in its supply chain, such as the risk of relying on a single logistics partner and warehouse. Advanced analytics could have also helped devise robust contingency plans, ensuring that even if one link in the chain broke, the entire system wouldn’t collapse.
In this article, we will explore the benefits of Manufacturing Analytics and its significant benefits to businesses.
What is Manufacturing Analytics?
Manufacturing analytics is a cornerstone of Industry 4.0, the next phase in the digitization of the manufacturing sector. We covered Industry 4.0 in our previous article and explored how it was becoming a widespread transition for businesses that were adopting automation and AI technologies.
Manufacturing Analytics, however, is more than just data automation. It involves using operational systems and machine-generated data to enhance various functions within a manufacturing company.
This data-driven approach aims to improve productivity, ensure product quality, optimize decision-making, and reduce operational costs.
The global manufacturing analytics market, valued at $5,950 million in 2018, is expected to soar to $28,443.7 million by 2026, growing at a CAGR of 16.5% from 2019 to 2026. However, how does manufacturing analytics work in enhancing supply chain analytics?
Manufacturing analytics acts as a critical enabler for operational optimization. It has transitioned from basic statistical evaluations to more complex, predictive analytical solutions that offer a deeper understanding of supply chain performance.
According to IBM, one of the current challenges is effectively utilizing the enormous volumes of structured and unstructured data generated within supply chain networks. Let’s understand the most important types of data within supply chain networks.
Data from the Lens of Supply Chain Analytics
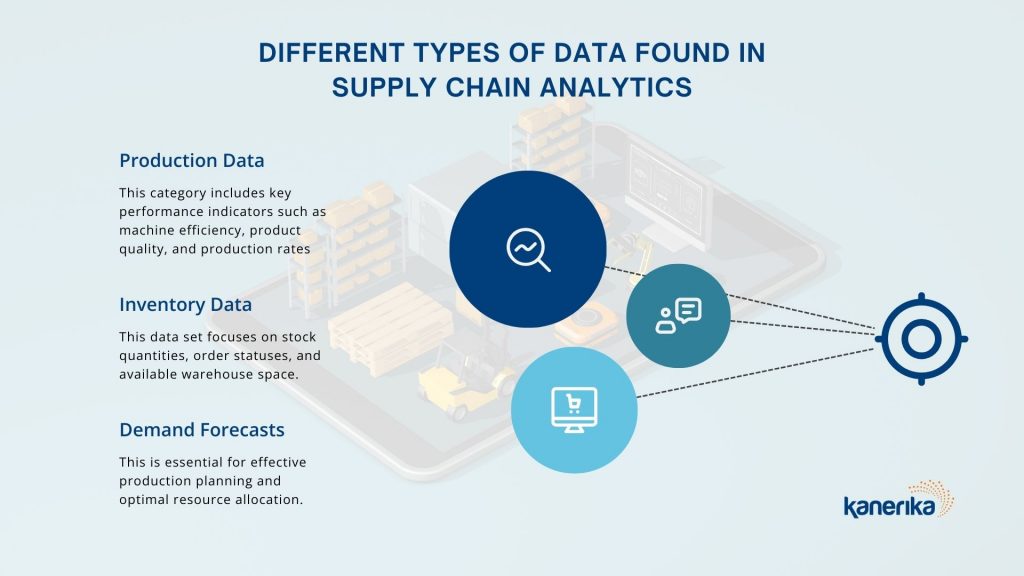
Production Data: This category includes key performance indicators such as machine efficiency, product quality, and production rates. Monitoring these metrics in real-time can lead to immediate adjustments, enhancing overall productivity and enabling maintenance through predictive analytics.
Inventory Data: This data set focuses on stock quantities, order statuses, and available warehouse space. By analyzing this data, companies can optimize inventory turnover rates and minimize the costs associated with holding inventory.
Demand Forecasts: Employing past sales data and market trends, predictive analytics tools can generate reliable demand forecasts. This is essential for effective production planning and optimal resource allocation.
Benefits of Manufacturing Analytics In Logistics
Manufacturing analytics has real-time uses in logistics and can offer numerous benefits to businesses, such as cost reduction and optimization of existing processes.
One example was our project with a leading US tourism and public transport provider. Amidst a significant decline in revenue due to the pandemic, the absence of a real-time, comprehensive view of marketing, sales, and product performance hindered our client’s effective decision-making.
Moreover, they had multiple data sources but lacked a proper data integration and analysis system. That was our first area to tackle.
Kanerika deployed a cloud-based, multi-tenant Business Intelligence system using MS Azure and Power BI. This system enabled real-time insights and data-driven decision-making.
The result allowed them resource scalability on demand, minimizing costs while maximizing profits. We were able to help them increase their profits by 17% and revenue by 26%.
Therefore, if we had to summarize our learning using manufacturing analytics across the supply chain and logistics industry, we’d categorize it into three distinct areas: cost reduction, revenue enhancement, and operational advantages.
A Buck Saved Is A Buck Made
In the manufacturing world, keeping machines running smoothly is crucial. Traditional maintenance programs have been more about reacting to problems than preventing them. While 80% of maintenance staff prefer preventive measures, manufacturing analytics is taking this to the next level.
How? Using real-time data, manufacturing analytics can predict when a machine will likely fail. This is a game-changer. It means technicians can fix issues at the best possible time, reducing production delays. Plus, it helps manage spare parts more efficiently, cutting costs.
This intelligent approach fits well with different types of preventive maintenance, like scheduled or predictive. Each type has its own rules aimed at preventing machine damage.
Personalized Warranty Achieved Via Manufacturing Analytics
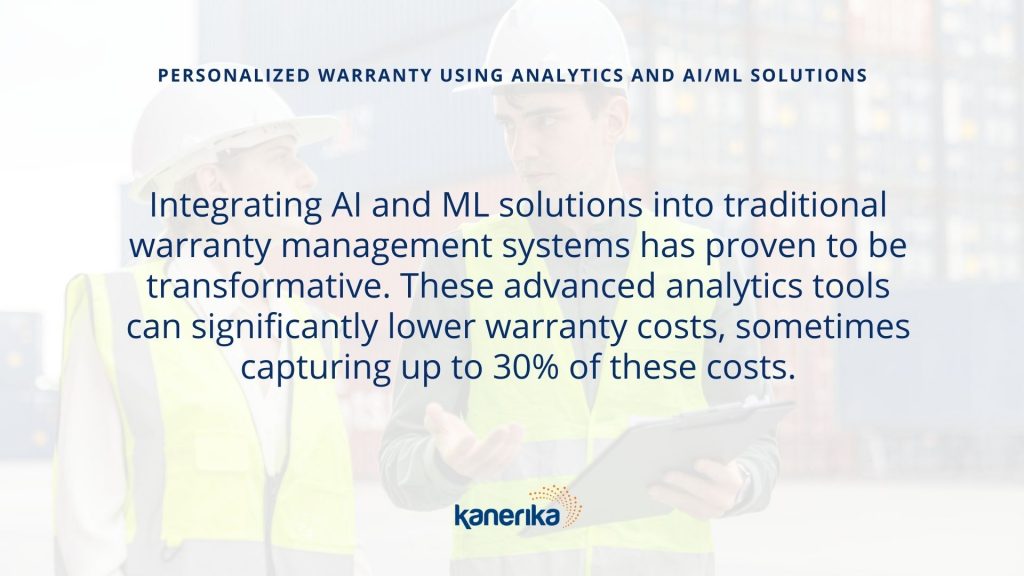
Traditional warranty models often adopt a one-size-fits-all approach, which can lead to unforeseen costs and inefficiencies. However, the integration of analytics into warranty management has revolutionized this domain. By leveraging real-time data from products currently under warranty, analytics enables a more nuanced and tailored approach to warranty management.
According to McKinsey, warranty costs can account for as much as 5% of product revenues in advanced industries. These costs weigh on net margins and impact overall business performance.
Integrating AI and ML solutions into traditional warranty management systems has proven to be transformative. These advanced analytics tools can significantly lower warranty costs, sometimes capturing up to 30% of these costs. This results in improved bottom-line profitability.
Gain Savings & Profits With Demand Forecasting Solutions
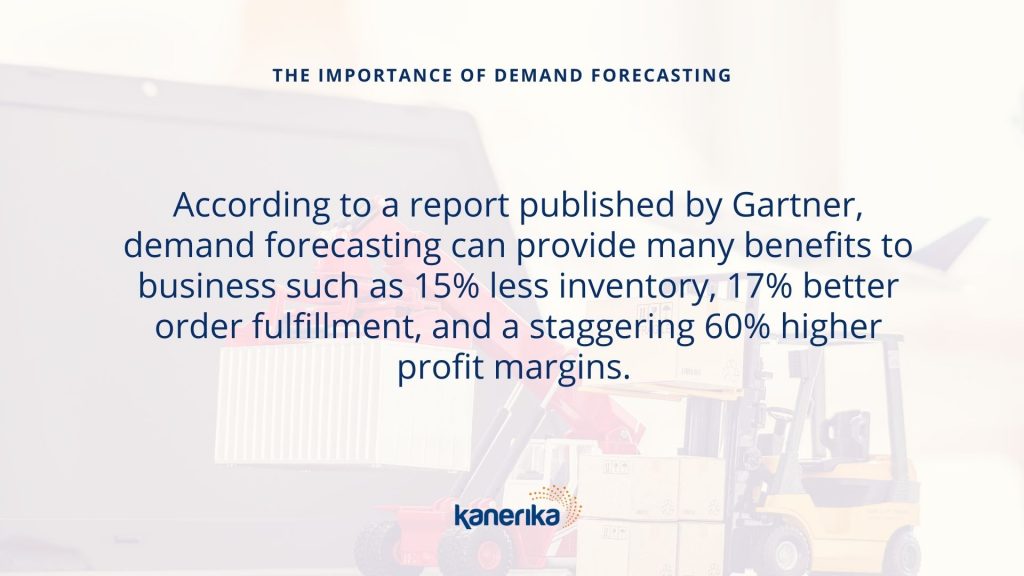
According to Gartner, companies that excel in demand forecasting experience many benefits, including 15% less inventory, 17% better order fulfillment, and a staggering 60% higher profit margins. These metrics are not just numbers but indicators of operational efficiency and business health.
Traditional demand forecasting methods often fall short in today’s volatile market conditions. Fortified with data science methodologies, manufacturing analytics provides an unparalleled, end-to-end view of the supply chain.
This results in a more efficient manufacturing schedule and an optimized inventory, reducing the risk of stock-outs or overstock situations.
The ‘Control Tower’ View To Curb Supply Chain Mishaps
We’ve come full circle, returning to the KFC debacle. This incident underscores that supply chain disruptions are inevitable in today’s volatile market, making risk management a critical focus. Enter the “control tower” approach, powered by real-time data analytics, which is a strategic asset for supply chain resilience. This centralized dashboard provides a panoramic and actionable view of the entire supply chain.
For instance, it integrates real-time data on materials in transit, such as location and estimated arrival time, into a single analytics platform. This enables rapid, data-driven responses to any disruptions, be they internal manufacturing issues or external factors like supply bottlenecks and geopolitical events.
Navigating The Implementation Highs & Lows Of Manufacturing Analytics
We have discussed in detail the benefits of analytics in manufacturing. Yet – implementing manufacturing analytics in your supply chain is a transformative but challenging endeavor.
One of the most critical aspects to consider is data quality. Inaccurate or incomplete data can skew insights and lead to misguided strategies.
Data integration poses another significant hurdle. The manufacturing industry often grapples with disparate systems—from ERP and MES to IoT sensors—that must be harmoniously integrated for a comprehensive view.
Given the technical complexities and the need for specialized skills to manage big data and ensure data security, this integration is often easier said than done.
Moreover, the success of any analytics initiative is highly dependent on the talent that drives it. Assembling a team of data scientists, analysts, and domain experts is essential but can be daunting given the specialized skill sets required.
The role of a data scientist, once dubbed “the sexiest job of the 21st Century” by Harvard Business Review, has become even more pivotal in the wake of accelerated digital transformations due to the Covid-19 pandemic. IBM had already forecasted a need for 2.72 million data scientists by 2020. “Then came Covid-19 and the shortage became even more obvious as digital transformations were put on fast forward,” noted Forbes.
In such a scenario, companies can struggle to hire suitable candidates to build their optimized workflows. This is where a consulting company like Kanerika can make all the difference to your business.
Kanerika: The Key to Seamless Manufacturing Analytics Implementation
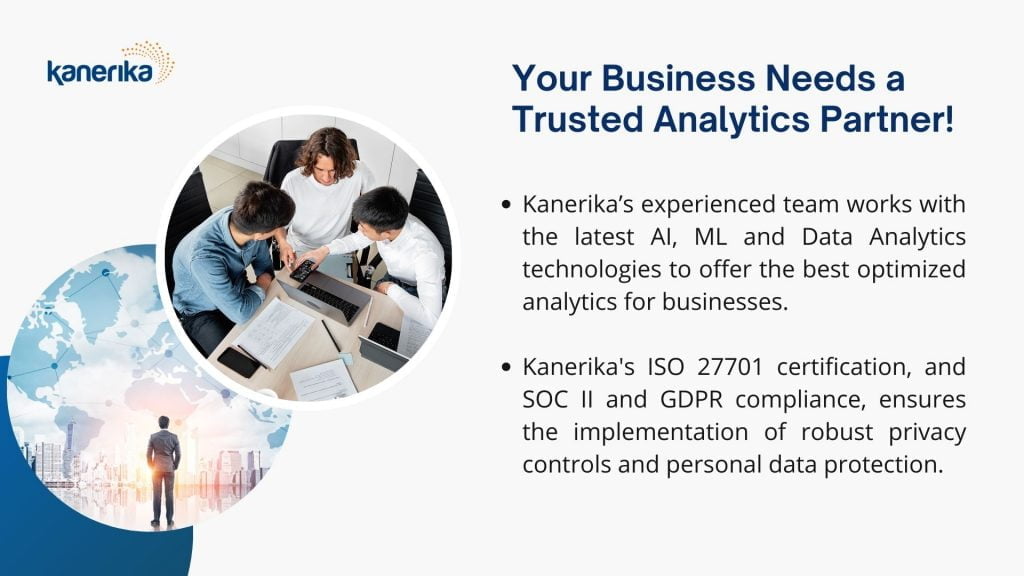
While the journey of implementing manufacturing analytics in your supply chain can be fraught with challenges, it’s not a path you have to walk alone. Kanerika has cracked the code to seamless implementation, leveraging 100 years of combined experience in AI, ML, and Data Analytics.
We customize our data analytics and integration services based on the unique needs of our clients, streamlining processes and reducing costs. Our track record speaks for itself—we’ve helped over 50 clients ease their data management and enhance business operations.
Take, for example, a recent case where the challenge was to automate an end-to-end supply chain workflow across multiple ERPs, including custom, Oracle apps, and Oracle Fusion. The manual process was tedious and prone to errors, consuming between 50 to 120 person-days every quarter.
The lack of a consolidated data center and the constant need for training new systems led to increased attrition and investment.
Kanerika stepped in with a solution that utilized UiPath and Oracle Fusion to automate the supply chain workflow. We orchestrated bots for sales order creation, purchase order generation, and fulfillment, thereby reducing delays and errors.
The result was a 32% improvement in resource optimization, a 60% reduction in errors, and a 78% improvement in process accuracy.
Partnering with Kanerka can help your business elevate with the right technology implementation and processes. Are you ready to grow your business with manufacturing analytics?
Book a free analytics consultation with us today!
FAQ
What is analytic manufacturing?
Analytic manufacturing uses data to optimize every step of production. It’s not just about collecting data, but actively analyzing it in real-time to predict problems, improve efficiency, and boost product quality. This involves sophisticated technologies and a data-driven culture to maximize production effectiveness. Think of it as manufacturing with the benefit of constant, intelligent oversight.
What is an example of manufacturing data analytics?
Manufacturing data analytics uses factory data (machine sensor readings, production logs, etc.) to improve processes. For example, analyzing sensor data from a bottling machine might reveal a pattern predicting upcoming malfunctions, allowing for preventative maintenance and avoiding costly downtime. This proactive approach optimizes efficiency and reduces waste. Ultimately, it helps make informed decisions to boost productivity and quality.
What is the meaning of manufacturing analysis?
Manufacturing analysis digs deep into how things are made, examining every step from raw materials to finished product. It’s about understanding efficiency, identifying bottlenecks, and spotting areas for improvement in the production process. Ultimately, it aims to optimize production, reduce costs, and enhance quality. This involves data analysis and process optimization techniques.
What are the 5 categories of analytics?
Analytics isn’t just one thing; it’s a spectrum. We usually break it down into five types: descriptive (what happened), diagnostic (why it happened), predictive (what might happen), prescriptive (what should we do), and cognitive (learning & adapting from data). Each builds upon the previous, moving from understanding the past to influencing the future. This framework helps businesses choose the right analytical approach for their needs.
What is GMP analytics?
GMP analytics uses data to ensure your manufacturing processes consistently meet Good Manufacturing Practices (GMP) standards. It’s not just about finding defects, but proactively identifying trends and risks before they impact product quality or compliance. This data-driven approach helps optimize processes, reduce waste, and ultimately, improve patient safety. Essentially, it’s using the power of information to guarantee consistently high-quality products.
What is big data analytics in manufacturing?
Big data analytics in manufacturing uses massive datasets (machine sensor readings, supply chain info, etc.) to optimize processes. It reveals hidden patterns and trends, allowing for predictive maintenance, improved quality control, and more efficient production scheduling. Ultimately, it boosts profitability by minimizing waste and maximizing output. Think smarter, faster, and more profitable manufacturing.
What is the role of data analyst in manufacturing industry?
Data analysts in manufacturing optimize processes and boost efficiency. They analyze production data to identify bottlenecks, predict equipment failures, and improve quality control. This leads to cost savings, increased output, and enhanced product reliability. Ultimately, they transform raw data into actionable insights driving better business decisions.
What is manufacturing data?
Manufacturing data is the heartbeat of a production facility. It’s the raw information – from machine sensors, quality checks, and production schedules – that reveals how efficiently and effectively goods are being made. This data provides crucial insights into everything from equipment performance to product quality and ultimately, profitability. Analyzing it allows for improvements in speed, cost and quality.
What is predictive analytics in manufacturing?
Predictive analytics in manufacturing uses data to foresee potential problems *before* they impact production. It leverages historical data, machine sensor readings, and other inputs to anticipate equipment failures, predict demand fluctuations, and optimize processes for higher efficiency and reduced downtime. Essentially, it’s about using data to proactively prevent issues rather than reactively addressing them. This leads to significant cost savings and improved product quality.